Pipe Fittings
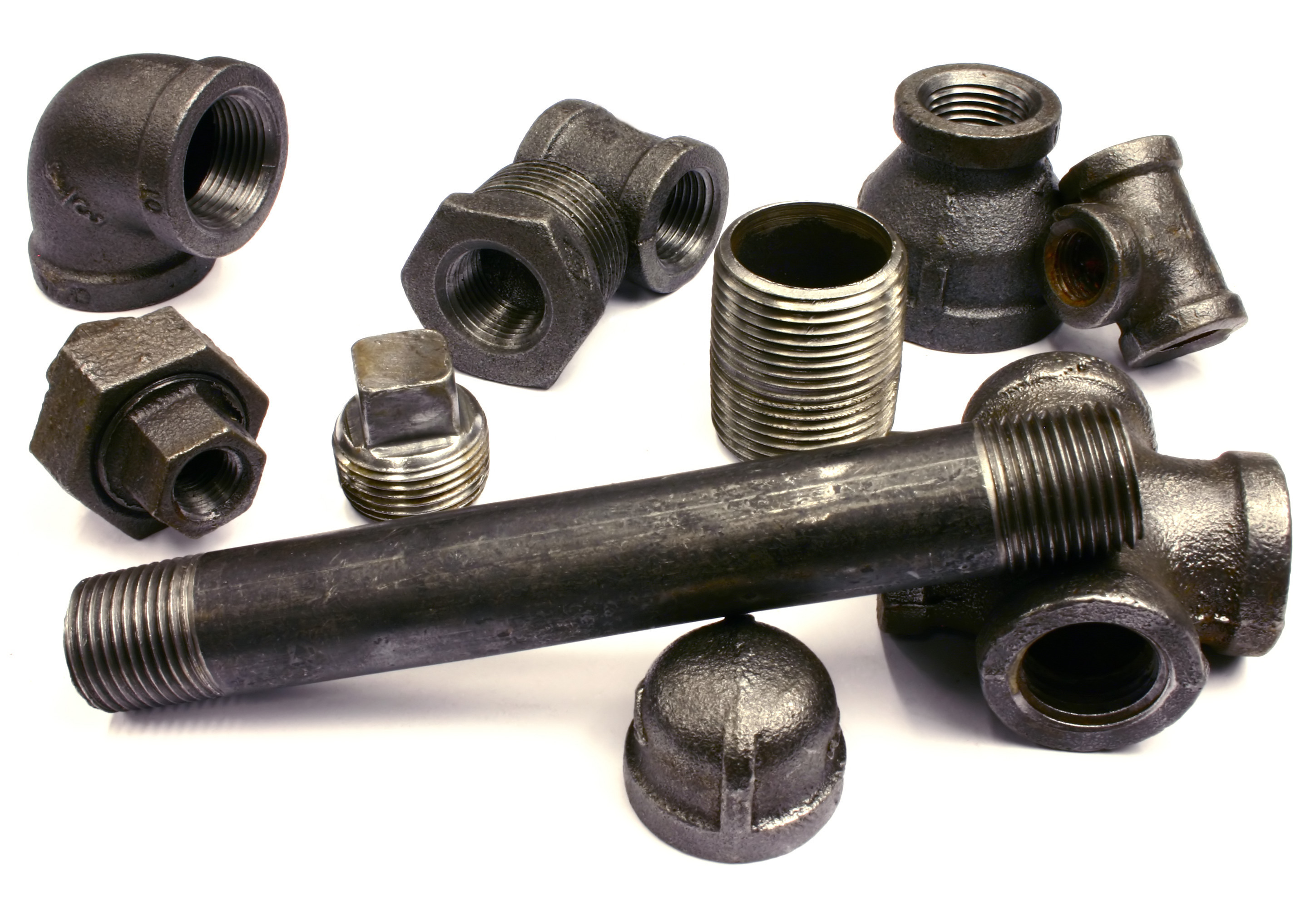


Carbon and alloy pipe fittings are essential components used to connect, control, and redirect the flow of fluids in piping systems. They are integral to various industries, including oil and gas, chemical processing, power generation, and water treatment.
Materials:
- Carbon Steel Fittings: Carbon steel pipe fittings are commonly made from materials such as ASTM A234 WPB (wrought carbon steel), which offer good strength and weldability at a relatively low cost. These fittings are suitable for general-purpose applications where corrosion resistance is not a primary concern.
- Alloy Steel Fittings: Alloy steel pipe fittings contain additional alloying elements such as chromium, molybdenum, or nickel to enhance specific properties such as corrosion resistance, high-temperature strength, or durability. Common alloy steel grades used for fittings include ASTM A234 WP5, WP9, WP11, WP22, and WP91, among others.
Types of Pipe Fittings:
- Elbows: Elbows are fittings that allow for directional changes in piping systems. They come in various angles, including 45 degrees, 90 degrees, and 180 degrees, and are used to redirect the flow of fluids around obstacles or corners.
- Tees: Tees are fittings with a T-shaped configuration that allow for the branching of piping systems into two or more directions. They are commonly used to connect pipes of different diameters or to create branches in pipelines.
- Reducers: Reducers are fittings used to connect pipes of different sizes, allowing for the transition between larger and smaller diameters. They are available in concentric and eccentric designs to maintain proper fluid flow.
- Caps: Caps are fittings that seal the end of a pipe, preventing the leakage of fluids and debris into the piping system. They are commonly used to cap off unused pipe ends or for temporary closures during maintenance and repair.
- Couplings: Couplings are fittings used to join two pipes of the same diameter in a straight line. They provide a secure connection while allowing for easy disassembly and reassembly of piping systems.
- Crosses: Crosses are fittings similar to tees but with a four-way configuration, allowing for branching in multiple directions. They are used in complex piping systems where multiple branches are required.
- Flanges: Flanges are external rims or collars used to connect pipes, valves, and other equipment to form a piping system. They provide a strong and leak-proof connection, typically through bolts and gaskets.
Applications:
- Oil and Gas Industry: Carbon and alloy pipe fittings are extensively used in the oil and gas industry for the transportation, processing, and distribution of petroleum products and natural gas.
- Chemical Processing: These fittings are employed in chemical plants for the handling and treatment of corrosive fluids and chemicals, where resistance to corrosion and high temperatures is critical.
- Power Generation: Carbon and alloy pipe fittings are used in power plants for steam, water, and coolant systems, where high-pressure and high-temperature conditions are common.
- Water Treatment: These fittings are utilized in water treatment facilities for the purification, distribution, and conveyance of potable water and wastewater.
Advantages:
- Strength and Durability: Carbon and alloy pipe fittings offer high strength and durability, ensuring long-term reliability and performance in demanding applications.
- Corrosion Resistance: Alloy steel fittings provide enhanced resistance to corrosion, erosion, and oxidation, making them suitable for harsh environments and corrosive fluids.
- Versatility: Carbon and alloy pipe fittings come in various sizes, shapes, and configurations to meet diverse application requirements, offering flexibility and adaptability.
- Compatibility: These fittings are compatible with a wide range of piping materials, including carbon steel, stainless steel, and various alloys, allowing for seamless integration into existing piping systems.
Carbon and alloy pipe fittings are crucial components in piping systems, facilitating the efficient and reliable transport of fluids across various industries. Their strength, durability, and resistance to corrosion make them indispensable for ensuring the integrity and functionality of piping infrastructure.